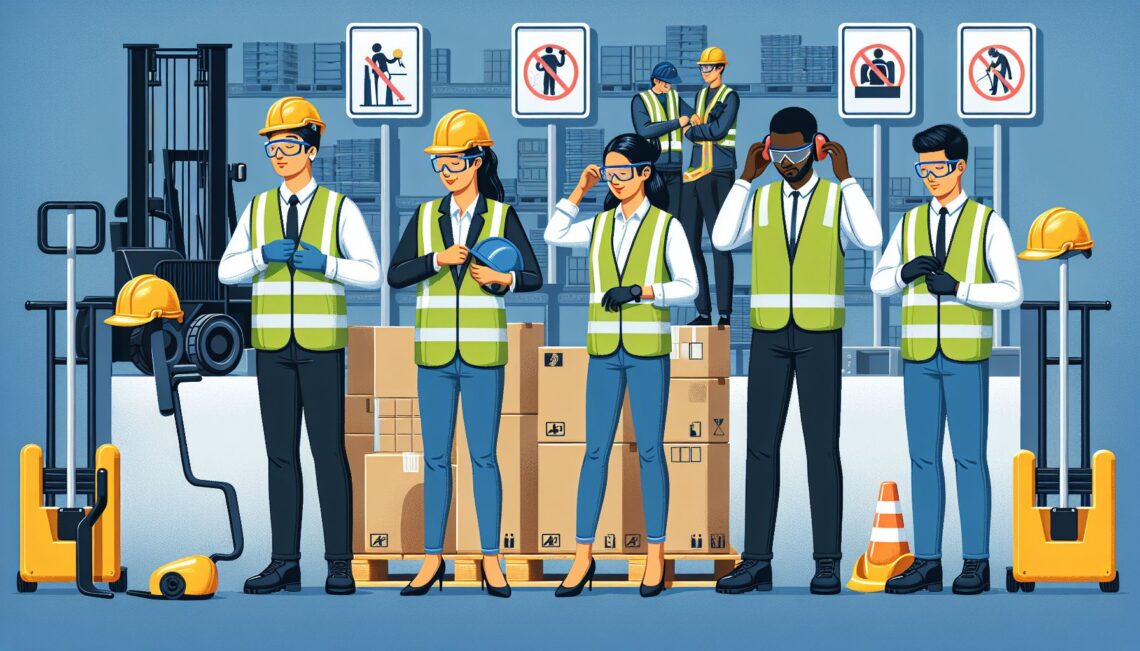
Essential Protective Equipment for Warehouse Employees
Working in a warehouse can be a physically demanding job that involves handling heavy objects, operating machinery, and navigating through potentially hazardous environments. As an employer, it is your responsibility to ensure the safety and well-being of your employees. One of the most effective ways to achieve this is by providing them with the necessary protective equipment. In this article, we will discuss some common protective gear that can significantly reduce the risks associated with warehouse work.
Head Protection
Head injuries are a serious concern in any workplace, and warehouses are no exception. Falling objects, low-hanging structures, or accidental collisions can all pose a threat to employees’ heads. That’s why it is crucial to provide them with proper head protection. Hard hats are a staple in warehouses, helping to absorb impact and safeguard against falling debris. Investing in high-quality hard hats that meet safety standards will keep employees safe and promote a culture of workplace safety.
Eye and Face Protection
Warehouses often contain various particles, chemicals, and objects that pose a risk of eye and face injuries. Employees should wear safety goggles, which protect against flying debris and chemical splashes. Additionally, face shields are recommended for tasks that involve grinding, cutting, or welding. These shields provide full-face protection and must always be worn when necessary to avoid potential injuries.
Hand and Arm Protection
Handling heavy objects, operating equipment, and working with sharp tools are activities that can put employees’ hands and arms at risk. Gloves are a fundamental piece of protective equipment that can reduce the likelihood of cuts, abrasions, burns, or exposure to harmful substances. Different tasks require different types of gloves, so it is essential to match the glove to the hazard. For example, cut-resistant gloves are vital when handling sharp objects, while chemical-resistant gloves are necessary for working with hazardous substances.
Foot Protection
In a bustling warehouse environment, foot injuries are a common occurrence. Employees must wear steel-toed boots or safety shoes to protect their feet from heavy objects, falling debris, or accidental impacts. Additionally, non-slip soles are crucial for preventing slips, trips, and falls, especially in areas where spills or wet surfaces are present. Proper footwear ensures that employees are well-prepared to handle any scenario and reduces the risk of injuries that could lead to productivity loss or long-term disabilities.
High-Visibility Clothing
Visibility plays a crucial role in preventing accidents, especially in busy warehouse settings where large equipment, forklifts, and vehicles are constantly moving. Employees should wear high-visibility clothing such as vests or jackets with reflective stripes. This ensures that they are easily seen by their colleagues and equipment operators, reducing the chances of accidents caused by limited visibility.
Conclusion
Keeping employees safe in a warehouse environment requires a proactive approach and appropriate protective equipment. Hard hats, safety goggles, gloves, steel-toed boots, and high-visibility clothing are essential gear that significantly reduces the risk of accidents and injuries. By providing employees with these protective tools, you create a safer workplace, promote a culture of safety, and demonstrate that their well-being is a top priority. Remember, work smart and prioritize safety to foster a productive and secure warehouse environment.
